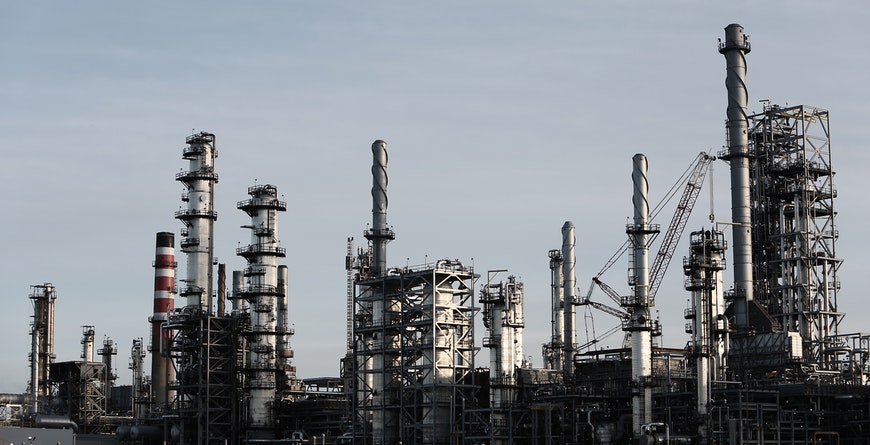
What is Programmable Logic Controller?
A PROGRAMMABLE LOGIC CONTROLLER (PLC) is an industrial computer control system that monitors input makes decisions based on its program to control outputs to automate a process or machine.
The automation of many different processes, such as controlling machines or factory assembly lines, is done through the use of small computers called a programmable logic controllers (PLCs). Ladder Logic is the most commonly used PLC programming language, it is not the only one. Ladder Diagram, Functional Block Diagram, Structured Text etc..,
Almost any production line, machine function, or process can be greatly enhanced using this type of control system. However, the biggest benefit in using a PLC is the ability to change and replicate the operation or process while collecting and communicating vital information. Another advantage of a PLC system is that it is modular. That is, you can mix and match the types of Input and Output devices to best suit your application.
What Is Inside A PLC?
The Central Processing Unit, the CPU, contains an internal program that tells the PLC how to perform the following functions:
Execute the Control Instructions contained in the User’s Programs. This program is stored in “nonvolatile” memory, meaning that the program will not be lost if power is removed
- Communicate with other devices, which can include I/O Devices, Programming Devices, Networks, and even other PLCs.
- Perform Housekeeping activities such as Communications, Internal Diagnostics, etc.
4 steps involved in the PLC operations:
1. Input Scan
Detects the state of all input devices that are connected to the PLC
2. Program Scan
Executes the user created program logic
3. Output Scan
Energizes or de-energize all output devices that are connected to the PLC.
4. Housekeeping
This step includes communications with programming terminals, internal diagnostics, etc…
There are four basic steps in the operation of all PLCs; These steps continually take place in a repeating loop.