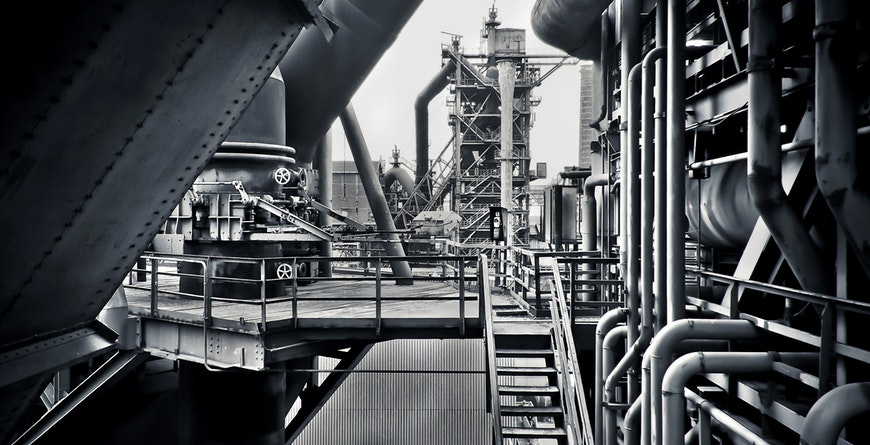
What is Piping and Instrumentation Diagram (P&ID)?
A P&ID (piping and instrumentation diagram), depicts the piping and other components of a process flow. P&ID commonly used in the automation and control system engineering field. It is used for modification and maintenance of the process flow that can be presented graphically. During the designing stage of the process, the P&ID diagram also gives the basis for the development of schemes, such as Hazard and Operability Study (HAZOP).
The diagram shows connection of equipment and instrument used to control the process. P&I diagram usually contains
- Instrumentation and designations
- Mechanical equipment’s
- All valves and their identifications
- Process piping, sizes, and identification,
- Vents, special fittings, drains, reducers, sampling lines, increasers, and swaggers,
- Flow directions, and Interconnections references,
- Control outputs and inputs, interlocks,
- Permanent start-up and flush lines,
- Interfaces for class changes,
- Annunciation inputs,
- Quality level,
- Computer control system input,
- Seismic category,
- Identification of components and subsystems delivered by others,
- Vendor and contractor interfaces,
- Intended physical sequence of the equipment
P&IDs are drawn at the early stage of design from a sequence of process flow sheet data, the mechanical process equipment design, and the instrumentation engineering design. In the design stage, the diagram provides the groundwork for the development of system control schemes, confessing for further safety and operational investigations, such as a Hazard and operability study (HAZOP).
The followed loop number is unique to that loop. For instance, FIC045 means it is the Flow representing Controller in control loop 045. This is also known as the “tag” identifier of the field appliances, which is usually given to the location and function of the instrument. The same loop may have FT045 – which is the flow transmitter in the same loop.