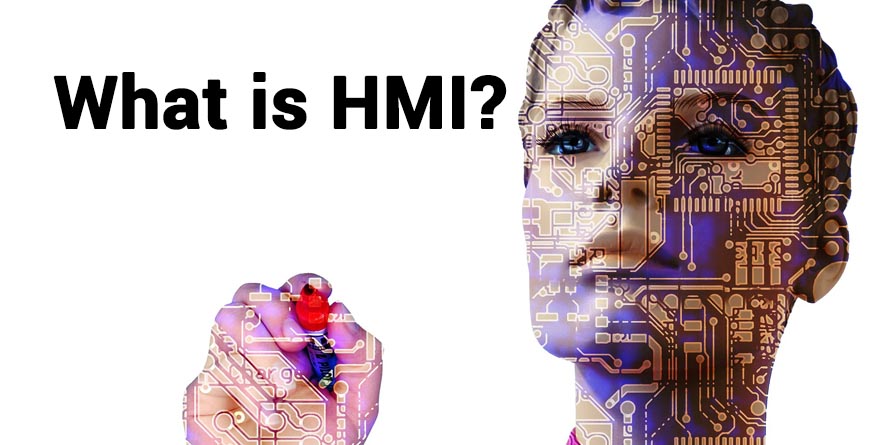
What is Human Machine Interface (HMI)?
What is HMI in Control Systems?
A human-machine interface (HMI) is the user interface that connects an operator to the controller for an industrial system. The term HUMAN MACHINE INTERFACE (or HMI) comes in picture when any human being comes in contact with a machine. The HMI is the primary tool by which operators and line supervisors coordinate and control the industrial and manufacturing processes in the plant. An HMI includes electronic components for signaling and controlling automation systems.
Let us know if there are additional points to be included in the comments section below after reading the article.
Before we look at the answer in detail, let us first look at the concept of man and machines.
The last few decades have seen high speed technological advancements and automation. In the field of industrial automation, HMI or Human-Machine Interface is amongst the hottest topics today. For this reason, it is imperative that all of us know what HMI is in the context of control systems.
Coexistence of humans and machines
Human beings and machines have co-existed for a long time now. Both have been evolving at a fast pace. Companies engaged in industrial automation have been working hard to have the best possible platform so that the two come closer quickly in a smooth way.
Control Systems
A system which manages, directs, commands or regulates how the other devices or systems behave is called a control system. Simple illustration is a home heating controller with a thermostat which controls a domestic boiler. On the other hand, large control systems are used in industries for controlling multiple processes or machines.
What is HMI in Control Systems?
HMI or Human-Machine Interface is a software application or user interface that enables communication of the state of a process to an operator and implementation of the operator’s control instructions by the industrial system. Typically, such information is displayed in a graphical format.
In simple terms, HMI or Human-Machine Interface in a control system is a software or a device that allows human beings or its users to communicate with various machines and productions plants in the system. It does so by converting huge amounts of complex data into accessible information. The operator thus has all the requisite tools to control the production processes.
The HMI provides Visual display of the process in Graphic / Digital / Animated form to give operators a clear and Real Time view of the process and Enables them to Issue commands / Load Set points / Modify sequences for controlling the process as required.
Although HMI is the most common term for this technology, it is sometimes referred to as Man-Machine Interface (MMI), Operator Interface Terminal (OIT), Local Operator Interface (LOI), or Operator Terminal (OT). HMI and Graphical User Interface (GUI) are similar but not synonymous: GUIs are often leveraged within HMIs for visualization capabilities.
Functions of HMI Software:
Monitoring: It is the ability to obtain and display plant data in real time. This data can be displayed as numbers, text or graphics that allow a reading easier to interpret.
Supervision: This function allows, together with the monitoring, the possibility of adjusting the working conditions of the process directly from the computer.
Alarm: It is the ability to recognize exceptional events within the process and report them
Control: It is the ability to apply algorithms that adjust the values of the process and thus maintain these values within certain limits.
Historian: It is the ability to display and store in files, process data at a certain frequency. This storage of data is a powerful tool for the optimization and correction of processes.
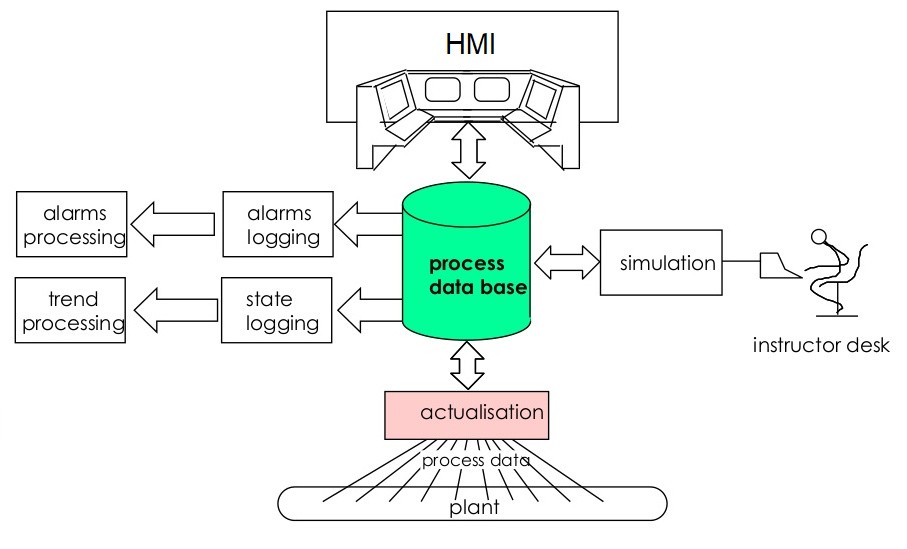
Types of HMI:
Developed to Measure: They are developed in a graphical programming environment such as VC ++, Visual Basic, Delphi, etc.
HMI canned Packages: These are software packages that cover most of the standard functions of SCADA systems.
Functions of HMI:
- Providing up-to-date plant information to operators through a graphical user interface.
- Translate operator instructions to the machine
- Engineering Development Station
Parts of HMI:
- Static and Dynamic Display
- Alarm Management
- Trending
- Reporting
HMI and Internet of Things (IoT)
Traditional HMI solutions were stand-alone, isolated terminals that were deployed by an OEM as part of a machine. New HMI solutions are either pre-configured to send data to the cloud or an on-premise solution. The IoT is changing manufacturing plants. More customers are expecting industrial HMIs to work like their cell phones in the way they interact with them. This is driving a big change in the perception of an industrial HMI and how it is expected to operate. With technologies such as Open Platform Communications Unified Architecture integrated into PC-based machine controls, it is possible to safely transmit encrypted data from the machine to the cloud and to enterprise level systems. The ability to push data to the cloud also enables engineers to integrate devices as smartphones or tablets, for example, to monitor machine and manufacturing data remotely, or simply take the HMI anywhere.
System Requirements for HMI
HMI solutions can be a stand-alone terminal base or fairly distributed for larger applications. The latter can involve server-grade hardware, a Microsoft server OS, and multiple nodes to load balance the application requirements. the display usually implements some sort of touch functionality, as this makes the HMI much more user-friendly; touch-type functions are generally very familiar to users.
Where can HMI be implemented?
HMI is implemented in any industry where human intervention with a machine or automated device is necessary. HMI is widely used in manufacturing—from the automotive industry to the highly regulated pharmaceutical and food industries. Process industries heavily use HMIs, such as in oil and gas, and mining operations in which many processes are managed remotely from a control room. The rise of Industry 4.0 and the Industrial Internet of Things has made this even easier, as we can turn our smartphones into a form of mobile HMI, and technology such as smartwatches has made HMI wearable, increasing accessibility and ease of use.
Advantages of HMI
The greatest advantage of an HMI is the user-friendliness of the graphical interface. The graphical interface contains color coding that allows for easy identification (for example: red for trouble). Pictures and icons allow for fast recognition, easing the problems of illiteracy. HMI can reduce the cost of product manufacturing, and potentially increase profit margins and lower production costs. HMI devices are now extremely innovative and capable of higher capacity and more interactive, elaborate functions than ever before. Some technological advantages the HMI offers are: converting hardware to software, eliminating the need for mouse and keyboard, and allowing kinesthetic computer/human interaction.
With remote access, the operator does not need to be anywhere near the automation line to start/stop or monitor production. With remote access, the operator can have all the same features, on your centralized unit in a smaller compact form. Simplicity is also a big factor in the usability of an HMI. The screens and functions provide for easy training to supervise the automation line.
Environmental Aspects for an HMI
The operating environment should always be considered when selecting an HMI. For example: for use in a warehouse that has excessive noise or vibration, one might decide on a heavy-duty HMI. If used in the food processing industry or somewhere that might need to be washed down, select a water-protected HMI. One must also consider temperature as a factor in the selection process. If used in a steel plant, next to a furnace, one would want something that can withstand extreme temperatures.