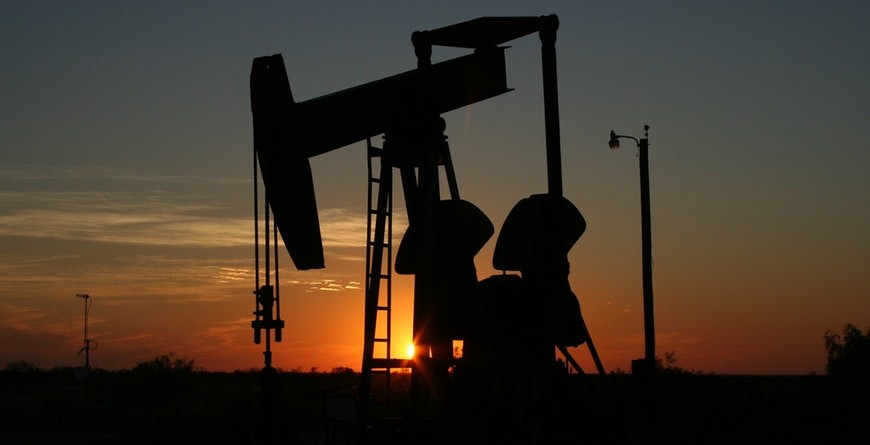
Process Control of Storage Tank after Downstream Section of Petroleum Industry
After completion of the refining of petroleum crude oil and of raw natural gas last part of the downstream process is storage of petroleum products, for that ambient pressure, temperature and level should be maintained. As like the midstream processes, this can also be made easy and accurate by applying industrial automation technologies.
For an example, a storage tank needs to maintain the ambient pressure of 1500 psi, petrol is volatile fuel, so there is a chance for an increase in pressure of the tank. Pressure can also be increased with increase in temperature. If such a situation occurs we can reduce the pressure by two ways, either we can decrease the volume by an outlet valve or open a top air vent. For simplifying the process we can also open the outlet valve and transfer some volume to another tank.
Inputs: High-Level Sensor(HLS), Low-Level Sensor(LLS), Temperature Sensor, Pressure Sensor
Outputs: Inlet Pump, Out Valve
High-level sensor and Low-level sensor check for the level of fuel; both work as discrete. If the low-level sensor is equal to one (ON) the inlet pump starts working and when the fuel reaches high-level sensor (HLS=1) the pump will stop. In between these process temperature and pressure is checked by the relative sensors.
If LLS=1 then pump starts
HLS=1 Pump stops
Pressure and Temperature sensors are analog sensors its output ranges from 4 to 20 mA, we use a function called Scale in PLC/DCS to change these analog value to our convenient range(normally 0 to 100), after that we can set a point, at which the sensor will be at on state.
So, if Temperature sensor or Pressure sensor equal to one the pump will stop and out valve will open.