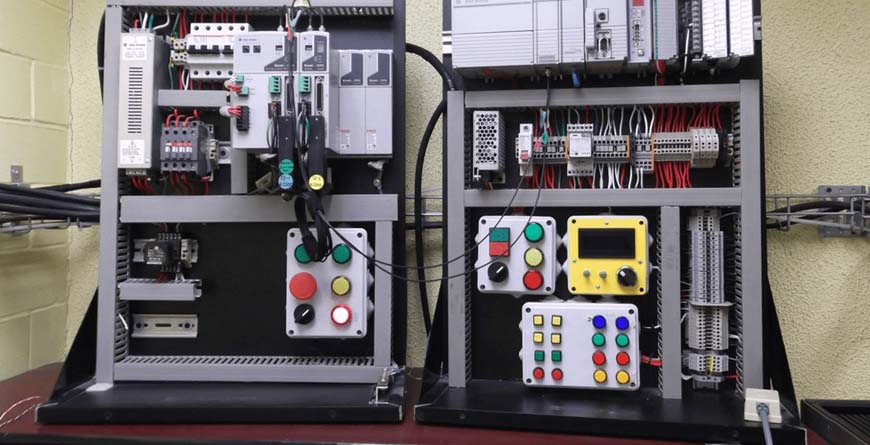
Fault Detection and Diagnosis for PLC
For every PLC controlled plant, the larger percentage of its faults are commonly in the actuators and sensors as well as its wiring and not in its PLC. The faults inside PLC are most likely in the output input power supply or channels rather than the CPU itself.
Case 1
Consider any output device that fails of turning on even the LED output is on. If you are testing the output PLC voltage and it indicates normality, then its fault may be the device fault or wiring fault. Then, if you will check the device’ voltage and indicates normality, then its fault is on the device.
Case 2
Failure of FED input for illuminating as required can be because:
- The device input it not properly operating
- The input device is not properly powered
- Improper wiring connection to input module or input module or LED is defective.
Most PLC are providing built- in procedures for fault analysis that carries out self- testing as well as display fault code. Together with brief messages that can also be translated through looking up codes in the list for giving the fault’s sources and the possible methods of recovery.
Here are the possible detection methods that can identify motor faults:
- Chemical analysis
- Current measurement
- Voltage measurement
- Partial discharge method
- Temperature measurement
- Vibration monitoring
- Radio frequency emission monitoring
- Speed measurement
- Acoustic noise measurement
Though induction machines can be reliable, they are also subjected with different undesirable stress that causes of failure in some faults. Because there are recent technology developments for Programmable Logic Controller (PLC), it is now commonly used in the different utility plant and industrial applications. One of it is using PLC for the fault diagnosis on IM. There are some researches that studied different machine faults which involves conclusions that machine failure includes installation and mechanical faults.
Today, the most commonly used part of Programmable Logic Controller (PLC) is its control units for industrial automation system. This PLC system is equipped of special I/O unit that is appropriate on the direct usage for industrial automation system. Input components like level, pressure and temperature sensor can also be directly connected on the input. Driver component like solenoid valves and contractors may be directly connected on the output. Most factories are using PLC for the automation process to lessen the cost of production as well as increase reliability and quality.
PLC can also be programmed to activate, sense and control the industrial equipment. So, PLC is incorporating number of I/O point that allows the electrical signal for interfacing. Output and input components of a certain process are connected on the PLC; control programs are loaded to PLC memory.
Different results showed that reliable PLC-based system for protection that includes operators and variable of IM has been developed. Using PLC can definitely reduce the cost for the implementation of new control circuit to the plant’ floor and reduces the needed time for making different changes up to relay circuit that is demanded by a certain process.